Sampler for Condensing Phases (Early Condensate, First Condensate) in Steam and Other Gases
The Sampler is used for troubleshooting corrosion and water and steam chemistry problems in steam turbines, feedwater heaters, BWR reactors, PWR steam generators, heat exchangers, piping, and geothermal systems. It can also be used for any other two-phase fluids (oil and gas, hydrocarbons, acids, etc.) for pressures up to 600 psi (4 MPa) and 600F (315C).
This instrument was originally developed for sampling moisture (early condensate, first condensate) from the wet steam regions of LP turbines and the extraction piping. Impurities and water treatment chemicals in the steam redistribute between the gas and liquid, often acidifying the water drops and film. The Sampler (Figure 1) samples wet steam from an extraction pipe and passes it through a high efficiency Moisture Separator (99.9%). The separated moisture contains the same concentration of impurities as is present in the liquid film that forms on LP turbine blades in the wet stages of the LP turbine.
The purpose of the sampling and chemical analysis of the steam moisture is to determine its corrosivity on the surfaces of LP turbine and other components which are in the wet steam regions, particularly the turbine blades and blade attachments and heat exchanger and piping surfaces. When used with on-line or grab sample analysis, the Moisture Sampler can be used to determine the pH, conductivity and concentration of impurities in the moisture.
Background
Flow-accelerated corrosion (FAC) is the combined actions of corrosion and erosion in the presence of a moving fluid (liquid water or wet steam), resulting in the loss of material and localized reduction of wall thickness. The geometry of each piping component and the temperature of the fluid are the major influences on the rate of FAC. The highest wear rates are around 150°C (300°F). Other variables that effect FAC are material composition (chromium, copper, and molybdenum), flow velocity and turbulence, and water and steam chemistry (pH, oxygen, oxygen scavengers).
Flow-accelerated corrosion has been experienced worldwide and can occur in virtually all types of nuclear units, fossil-fired units, and industrial steam systems. Both nuclear and fossil power plants have had fatalities caused by FAC as the initiator. Damage from FAC has occurred in virtually every high energy water and steam/water system in a power plant.
Any carbon steel piping system with the correct thermodynamic conditions may experience FAC. In utility and industrial power plants, systems that are commonly susceptible to FAC include turbine condensate and feedwater piping, return condensate piping, feedwater and other heater drains, and deaerator vessel shells.
The susceptibility of a system to FAC can be reduced by controlling the pH and oxygen concentration of the water. Periodic inspections are performed to determine the remaining wall thickness of susceptible components. These inspections are costly and time consuming and often require the unit to be out of service for the entire time of the inspections.
Description
The Sampler (Figure 1) collects samples of the moisture in the wet steam. The steam is removed from the piping at an isokinetic sampling rate. It then passes through a moisture separator that removes 99.9% of the moisture and water droplets greater than 1 micron while allowing the steam to pass. The separated moisture drains through the bottom of the separator, passes through a sample cooler and can then be sent to on-line analyzers, directly sampled, or sent to a drain. The saturated steam exits the separator and passes through a condenser after which it is sent to drain. Flowmeters are installed on the condensed steam and separated moisture drain lines in order to calculate the % moisture in the sampled steam.
In order to achieve the greatest accuracy, it is recommended to sample the wet steam using an EPRI Isokinetic Sampling Nozzle. This will result in a sample that is representative of the conditions in the pipe. If a surface tap is used, the surface liquid film on the inside diameter of the pipe will be sampled.
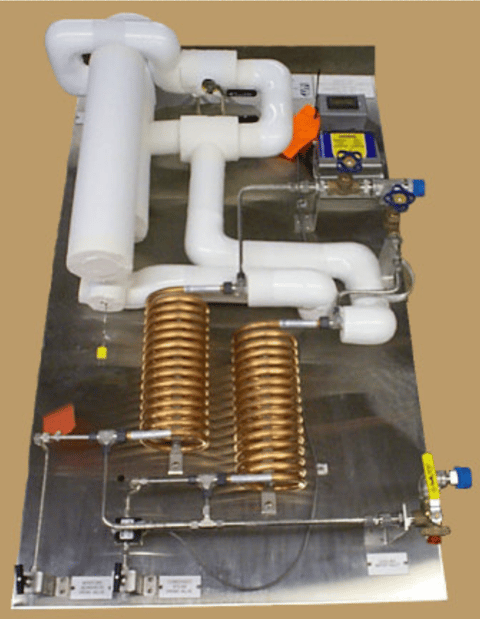
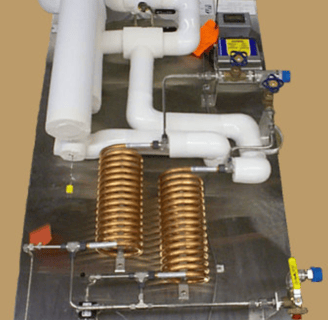