Nitrogen Sparging and Blanketing of Water Storage Tanks
Background
Scale and Corrosion
Currently, after outages, many boiler and pre-boiler systems are filled with aerated water, sometimes containing high ppm concentrations of ammonia and hydrazine. This water, which is exposed to air in vented storage tanks, contains high concentrations of carbon dioxide, carbonates, and oxygen. The practice of dosing the tanks with ammonia and hydrazine may reduce the oxygen concentration, but it increases, by about 10 times, the concentration of carbonate due to the formation of ammonium carbonate.
While this water is being pumped into the system and heated during startups, the ammonium carbonate breaks down, elevating the concentration of carbonic acid and reducing the pH in the feedwater and boiler. In room-temperature laboratory samples, an alkaline pH is misleading because it does not represent the actual pH at the temperatures in the boiler.
Filling the boiler and preboiler with aerated water results in large variations of pH and oxygen concentrations. These variations influence the solubility of iron and copper oxides; solubility is high at low pHt (pH at temperature) and low at higher pHt. During startup and normal operation, CO2 is driven out and the oxides which dissolved after boiler fill and warm-up then precipitate and form deposits. A high concentration of oxygen and low pH during the startup period enhances corrosion of the economizer and other components, generating additional corrosion products, which later deposit.
Exhaustion of Condensate Polishers
Adding aerated makeup during startups and operation causes exhaustion of condensate polishers by carbonates and elution of already exchanged impurities. This is especially a problem in steam cycles with high makeup requirements, such as in cogeneration cycles.
Advantages of Nitrogen Sparging and Blanketing
Filling the boiler, deaerator, and feedwater system with deaerated water with low concentrations of oxygen and carbon dioxide leads to minimization of iron and copper oxide scale and corrosion, faster startups (less iron and copper holds), and lower frequency of chemical cleaning.
Using deaerated makeup reduces exhaustion of condensate polishers by carbonates.
No need for auxiliary steam for deaerators - energy saving.
Reduction in use of oxygen scavengers - less environmental impact, less organic breakdown products (organic acids, CO2), lower costs.
Elimination of storage tank contamination by dust, no organic growth, no cleaning.
Desctription
The nitrogen system design is shown in Figure 1. It is a schematic diagram of a tank with the Bottom Sparger (A), Inlet Pipe Sparger (B), Nitrogen Supply and Controls (D), Oxygen or Conductivity Analyzer (F), Tank Pressure Control (C), and an Overflow Pipe (E)). The sparging itself is through sintered stainless steel Sparging Elements. The pressure to the sprayers is controlled by two pressure regulators; one for the Bottom Sparger and one for the Inlet Pipe Sparger, followed by a passive critical orifice flow element which guarantees that the nitrogen flow will never exceed the capacity of the tank pressure control siphon, which vents the excess pressure. The length of the sparging time is based on oxygen concentration at the bottom of the tank or conductivity (mostly elevated due to carbon dioxide).
Anticipated Performance
The Nitrogen Sparging and Blanketing System will maintain oxygen concentration in storage tanks at less than 300 ppb and conductivity less than 1 uS/cm. These parameters are maintained during pumping in, pumping out, and water storage without pumping, even when the tank capacity is exceeded and a larger volume is required.
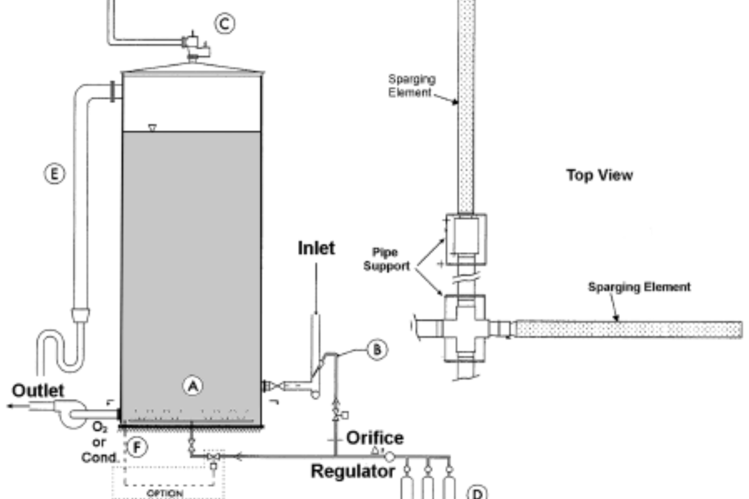
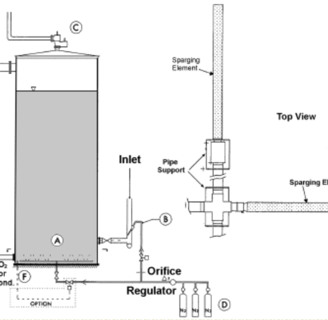