Evaluation for Flow-Accelerated Corrosion (Erosion-Corrosion) for Nuclear, Fossil, and Industrial Steam Generation
Background
On December 9, 1986, a rupture occurred in an 18-inch diameter elbow in the feedwater pipe leading to the main feed pump "A" of Virginia Power Surry Unit #2. The "break before leak" demonstrated itself as the separation of a large piece of the carbon steel elbow, which was found to have been significantly weakened by wall thinning caused by flow-accelerated corrosion (FAC, E-C).
In 1995, a fatal pipe break at the economizer inlet occurred at a Wisconsin utility and in 1996 at a Wisconsin paper mill. An industry survey revealed that wall thinning by flow-accelerated corrosion, as well as formation of excessive amounts of corrosion products in the steam cycle is a widespread problem. Almost 100% of PWR unit wet steam and 50% of preboiler systems, 30% of fossil, and 40% of industrial units in the U.S. are affected. Flow-accelerated corrosion is also very common in the combined cycle units in piping and HRSGs. It can lead to catastrophic failures, leaks in feedwater, wet steam, and condensate piping, interference with proper cycle chemistry control, and accumulation of corrosion products in steam generators, turbines, and on heat transfer surfaces.
Using various sources of field and laboratory data, Jonas, Inc. has developed an evaluation procedure as described below.
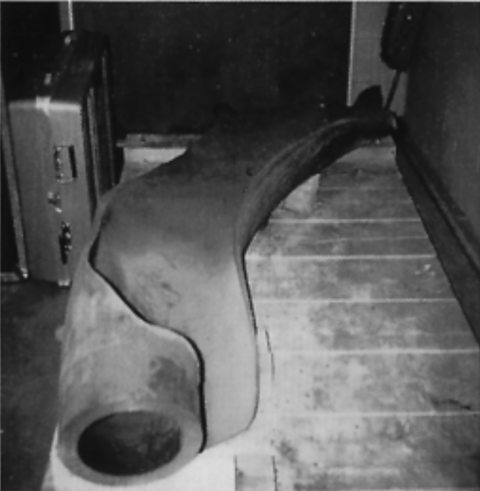
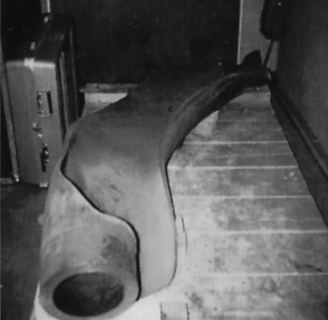
Figure 1. Example of Failure due to Flow-Accelerated Corrosion
Evaluation of Combined Effects:
Component Geometry
Flow Velocity
Water and Steam Properties
Material Composition
Water Chemistry
Operating Experience
Objective of the Evaluation:
Find and Select Components to be inspected
Interpret NDT Results
Find Causes of Wall Thinning
Determine Inspection Interval
Determine Effect of Cycle Iron Transport
Recommened Engineering Solutions
Project Task (one or more)
Preliminary assessment (drawings, flow velocities, cycle design, experience)
Component details and actual installation (walkdown, assembly, past history)
Final system and/or component description and operating and inspection/maintenance history
Computer modeling, calculation of erosion-corrosion rates, contributions of individual effects
Monitoring of wall thinning rate
Report with conclusions and recommendations
Implementation of engineering solutions
Follow-up